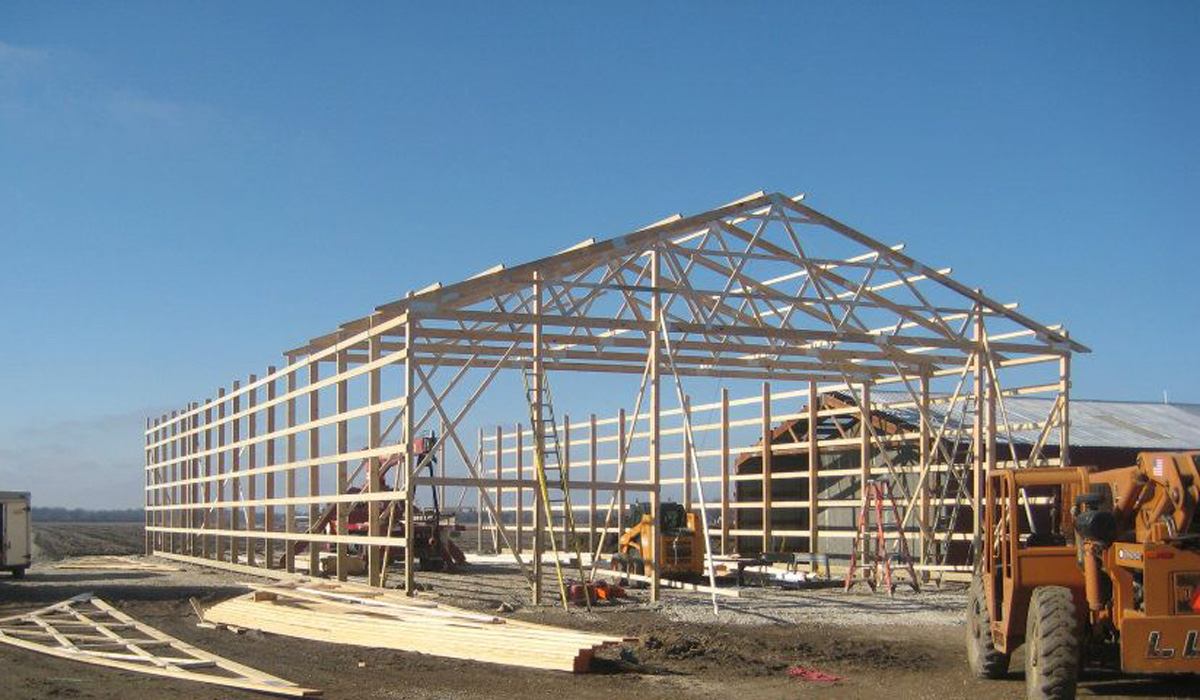
POST FRAME CONSTRUCTION – BUIDLING A BARNDOMINIUM
WHY YOU SHOULD CONSIDER POST FRAME CONSTRUCTION
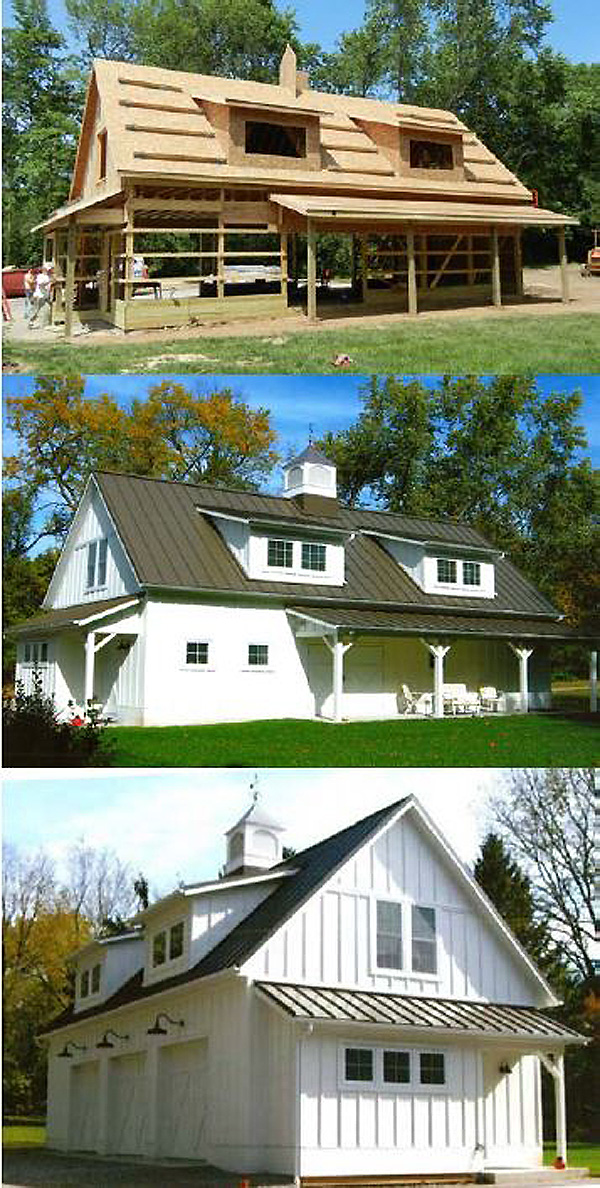
AN ECONOMICAL OPTION TO TRADITIONAL FRAMING
If you are looking to build a cost effective building using post frame construction, such as a home with an extended garage or shop, there are several details to consider in the architectural design and engineering. Post frame buildings are engineered with wood frames, and use laminated columns instead of steel or concrete to support the roof structure. Compared to some other building types, post frame buildings are a relatively simple concept.
Post frame structures are more quickly erected than other kinds of buildings. Because the larger posts and the interlocking frame can handle greater loads than stud-wall construction, fewer structural materials are needed, which saves time and other costs. Also, because posts are spaced farther apart than studs, post-frame buildings feature an exceptionally large wall cavity and provide ample room for insulation, lowering heating and cooling costs through the life of the building.
Almost any type of exterior façade may be installed on post frame buildings, which can be designed to meet the highest standards for quality and aesthetics. Post-frame construction is an efficient and economical option for low-rise applications and is now the construction method of choice for any number of residential, commercial and agricultural projects.
Today, post frame construction is being utilized to construct everything from fire stations to schools to car dealerships and more. The frame building system boasts less load bearing walls, fewer trades needed for construction, and faster build speed. These valuable attributes are the main reasons why previously unheard of designs are now being implemented with building frame systems.
There are four different types of post frame construction: suburban, commercial, equestrian and agricultural. The most important part of the design is to not underestimate the power of wind. As wind blows, it places a tremendous amount of pressure on everything in its path – and only properly engineered buildings will be able to handle it. Code buildings are designed to withstand 90 mph of straight-line winds. But if you live in an area where winds will exceed that speed, or where they’ll be extended, you need to design your post-frame building accordingly.
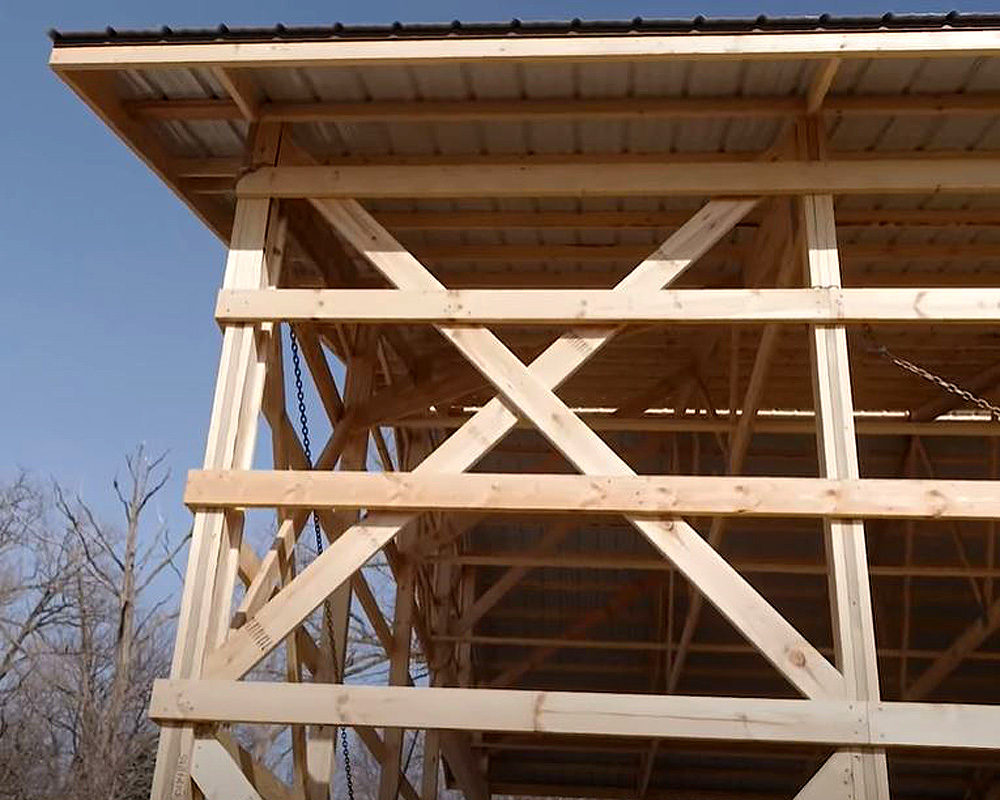
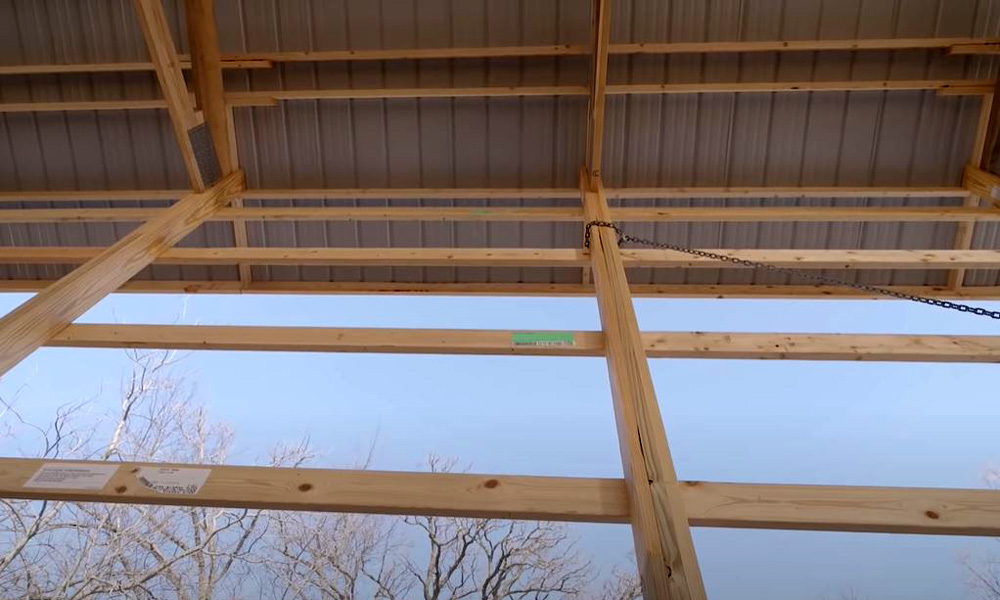
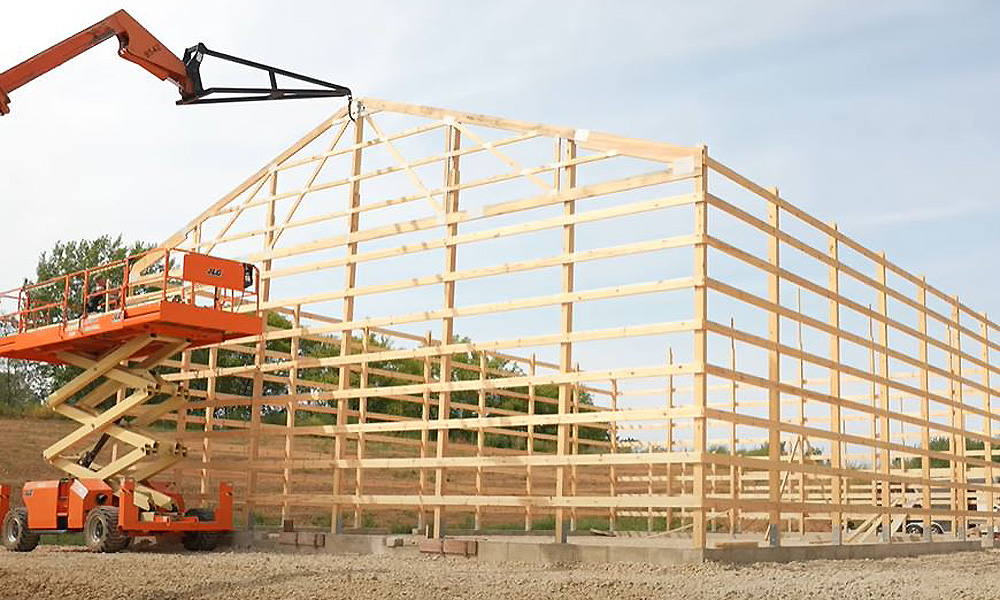
Post frame buildings use load bearing post to support the roof system, rather than the traditional 2x stud framing like you may find used on a house. There are many, many ways of designing and constructing a post frame building so this guide will only show a few examples of common post frame construction. Please check with your local building codes before using any of this information.
Understand the building codes of your city or state. Codes vary depending where you live and per type of building. For instance, a commercial building will have different design requirements than a simple storage space, due to it having a greater people occupancy. Other critical components are assessing snow loads, frost depth, and soil conditions. Figuring out these environmental conditions and stresses will determine which materials you use, how these materials are engineered to fit together and how columns (posts) are placed into the ground or attached to the foundation.
STRUCTURAL COMPONENTS
Pressure Treated Lumber: Treated lumber is primarily used for skirt boards and post. Generally, any lumber within 18” from the ground should be treated. 2”x_ skirt board or any board in contact with the ground should have a min. of .40 for ACQ and .15 for CA-C. Treated lumber installed higher than 18” above ground may be a lower retention.
Fasteners: Fasteners used with treated lumber should be corrosive resistant. Stainless steel or hot-dipped zinc-coated galvanized steel are often used with treated lumber. For best results, use the same type of metal for fasters as the metal siding and trim.
Posts: A structural wood column. It functions as a major foundation element when it is embedded in the soil. Post frame building posts include solid-sawn posts, structural composite lumber posts, glulam posts, mechanically-laminated lumber posts, and poles.
Post Footing: Concrete footer pads, usually 18”-24”, are placed at the bottom of the hole below the wood post. All concrete footers should be mixed with clean water outside of the hole, and set before the post is placed. Building size, height and other load factors will determine the pad size required, but generally the depth of the pad is half the diameter of the pad.

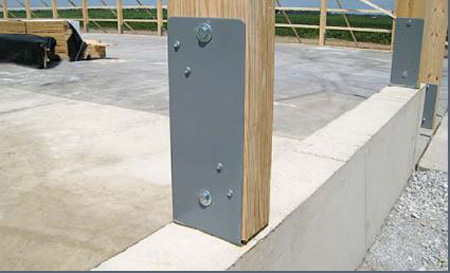

Skirt Board often called Splash Board or Grade Board may be one or more rows of treated 2×6, 2×8. The bottom of any siding or wall sheathing will be attached to this. If steel siding is fastened directly to the treated skirt board, a barrier of: building felt, house wrap, window wrap or other non-metal flashing is recommended between the two.
Girt: 2×4 or 2×6 horizontal framing member nailed from post to post. Girts are perpendicular to post. Spacing is usually no further than 2’ on-center.
Top Girt or Truss Carrier: Highest girt from ground level. In weight bearing cases (where a truss is not attached directly to a post) the girt acts as a beam and often labeled as a “truss carrier”.
Trusses: often spaced 4’ to 10’ on-center, trusses may spaced the same as and attached directly to the post, or spaced differently than the post and attached to a truss carrier beam that spans between the post. For shorter roof spans, 2x_ rafters are typically spaced 18”-30” on center.
Purlins: roof purlins are 2×4, 2×6 or 2×8 lumber that spans between the trusses to provide framing for metal roofing or roof sheathing. May be attached above the trusses on-edge or flat, or between the trusses using post frame anchors or joist hangers. Spacing will vary be design and roof load, but usually 24” on-center or less.
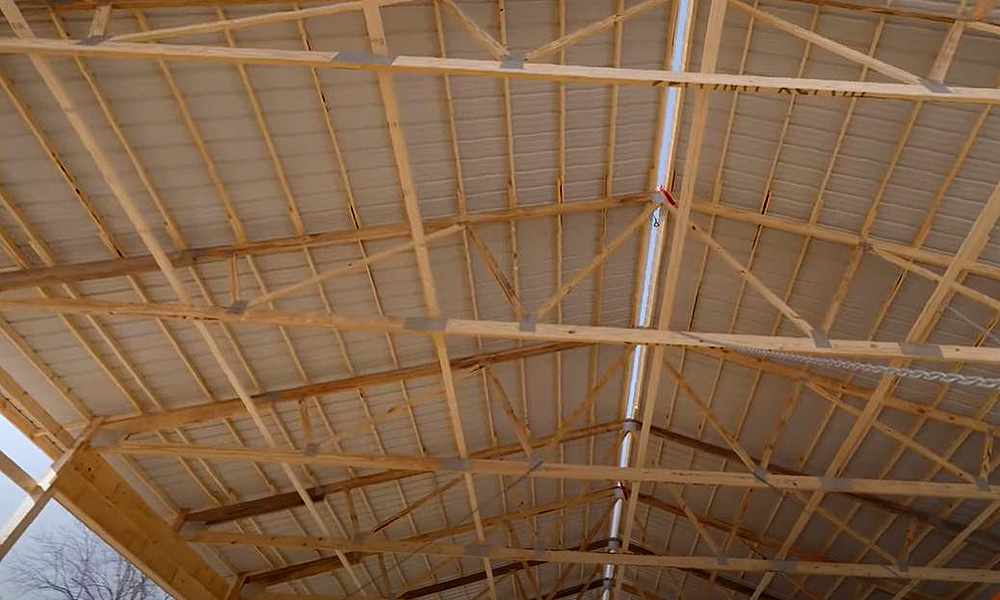

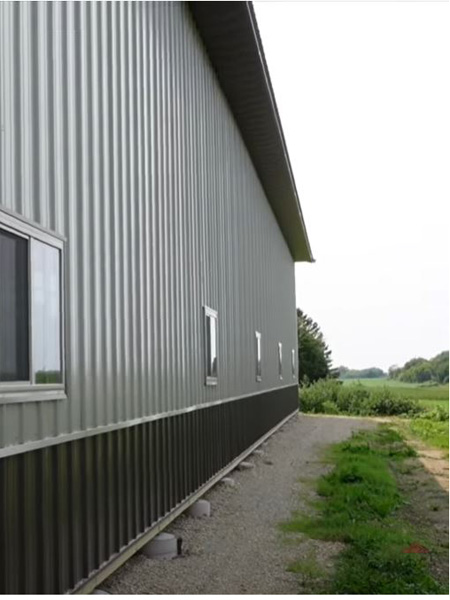
Siding: 29 gauge painted ribbed steel siding is one of the most common siding options for post-frame buildings. Offered in a variety of colors and ribbed patterns, it may be applied directly to the wall girts. Corrugated galvanized steel (unpainted) is an economical choice, but does not have the durability of the painted metals. Metal siding should not touch ground. Sheathing (OSB or plywood) may be applied over the girts and other sidings such as: vinyl, stucco, stone veneer, lap, panel, wood, etc. may be applied.
Roofing: As with siding, 29 ga. Painted ribbed steel is the most common roof covering. Purlins may also be covered with a sheathing and shingles and other roofing products may be used.
Most metal companies require support for metal roofing or siding at a maximum of 2’, therefore wall girts and roof purlins should also be spaced no farther than 2’ o.c. or as required by design.
